
HARDENING
Induction hardening
In induction hardening, the areas to be hardened are heated using induction current and then quenched using a water spray if required.
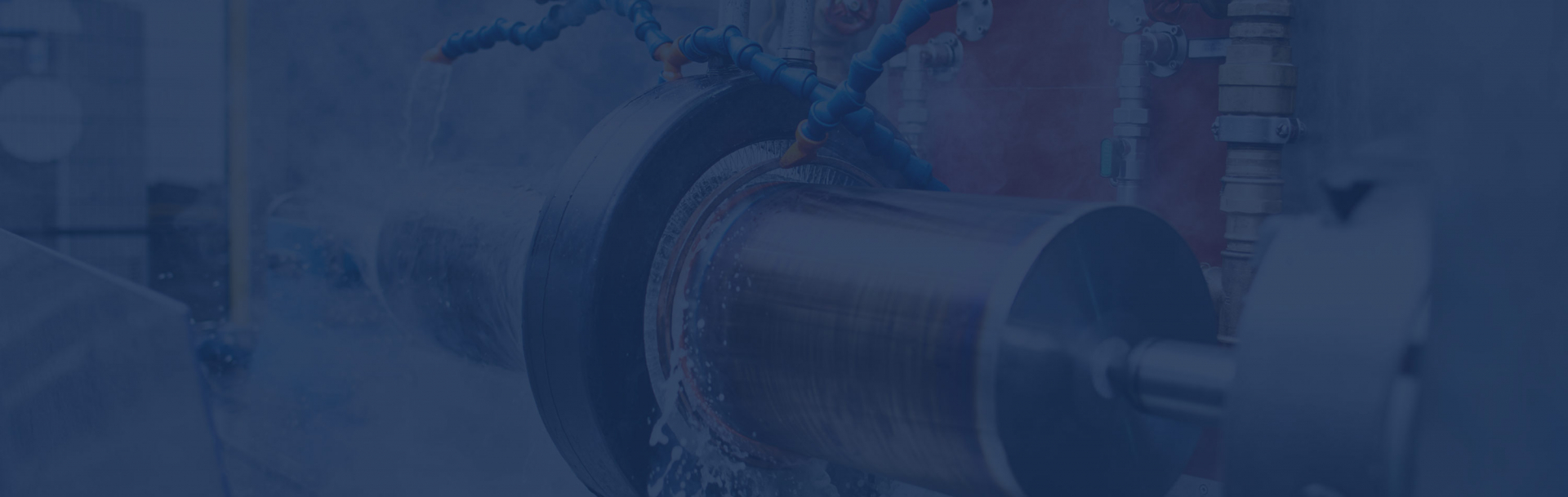
Advantages of the process
Precise
Control
The entire process is customised to a single workpiece so that even components with complex geometries can be hardened.
Hardening of
partial areas
Precisely defined areas of the component can be hardened with low distortion, while the core structure remains unchanged.
Outstanding
component properties
Induction hardening produces components with high fatigue resistance and improved wear resistance in selected areas.
Any
component size
As no furnace is required for induction hardening, even very large components can be processed without any problems.
Technical!
Components Induction hardening:
- Bolts, axles and shafts up to Ø 300mm x L= 3000mm
- Rotation circulation hardening, feed hardening and mould inductor
- Hardening of gear wheels rotation rotation up to Ø 300mm
- Hardening of gears single tooth hardening up to Ø 600mm
- Hardening of gear racks, rails and rails, forced hardening if necessary
Technical!
Process Induction hardening:
- Mould inductor , Ring inductors , Special inductors , Large number of inductors available , Self-made
- RHT HF 0.8mm to 2mm
- RHT MF 1.5mm to 6.0mm
- Reproducible process as inductor and parameter are defined and stored in NC
- Between centres such as tailstock and chuck, rotary table, magnetic table and T-slot table
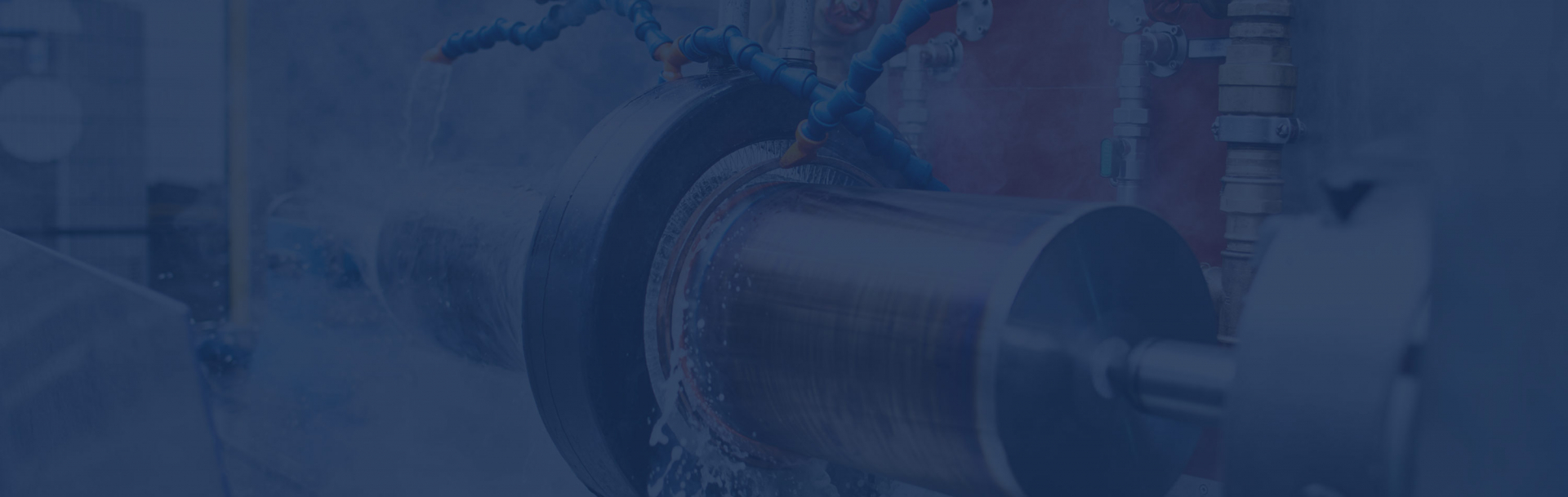
Hardened surfaces are subjected to stresses such as guides, bearing seats, sealing seats, radial shaft seal seats, gearing and external pressure gauges under load and torsion. Materials generally carbon steels from 0.30 C, heat-treatable steels, alloyed steels, X-steels, tool steels, stainless steels, valve steels and cast iron (by arrangement).
Heat treatment using induction current
Induction hardening is used to improve component properties by partially increasing the surface layer hardness and is ideal for highly complex or particularly bulky components.
While a large number of workpieces are hardened simultaneously during case hardening, induction hardening focusses on the individual part. The entire hardening process - from the inductor to the energy and frequency applied to the quenching and tempering process - is specially customised to the component in question. For this purpose, the areas to be hardened are heated using an inductor, a coil made of copper.

Precise process for components
The alternating current flowing through the coil generates an alternating magnetic field that heats the component to its transformation temperature.
If the heat can dissipate quickly enough into the rest of the still cold workpiece, quenching is not necessary afterwards.
This is an extremely precise process that is preferably used for components that are exposed to high loads. Induction results in an excellent surface hardness with a high case-hardening depth, which gives the component resistance to extreme loads.

The soft core and extremely hard outer layer improve fatigue resistance.
These properties are particularly important for components that are subject to torsional stress and for surfaces that are subject to impact forces. The process can only be used for materials with a carbon content of more than 0.35 per cent.

Kennzahlen
Temperature:
individual
Lead time::
from 72 h
Hardening depth:
up to 6 mm
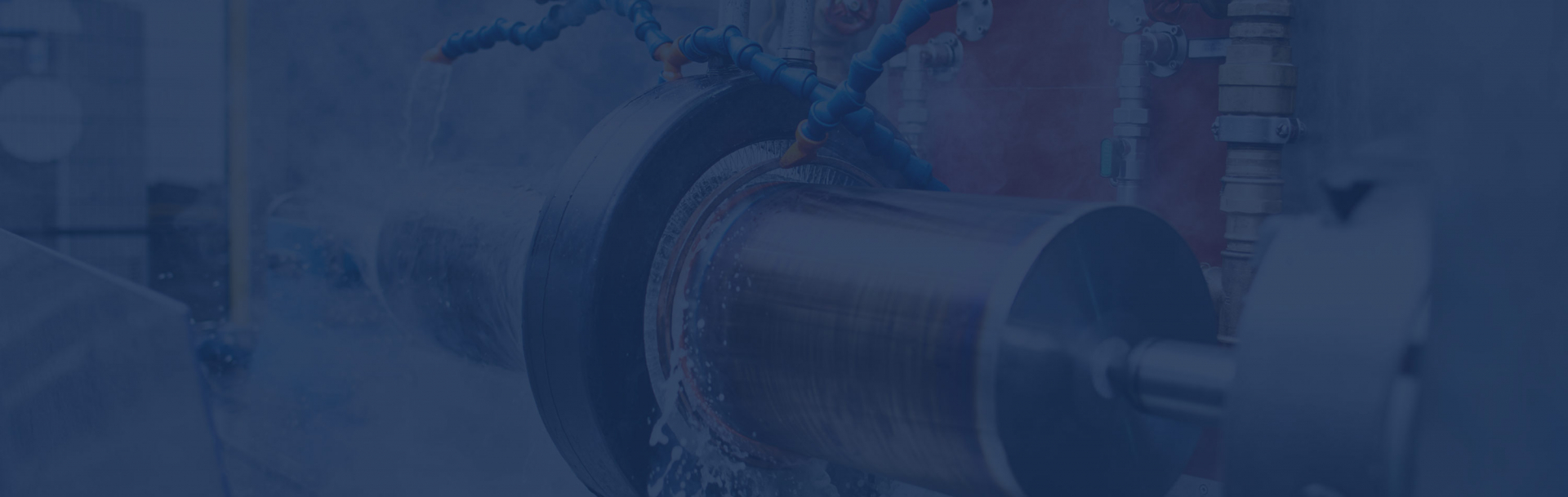
Get a quote
Request a free and non-binding
offer from us now!
Information!
For the preparation of your individual offer
we need the following information from you:
- Material
- Surface hardness and hardening depth
- Hardness range
- Weight and quantity
- Dimensions
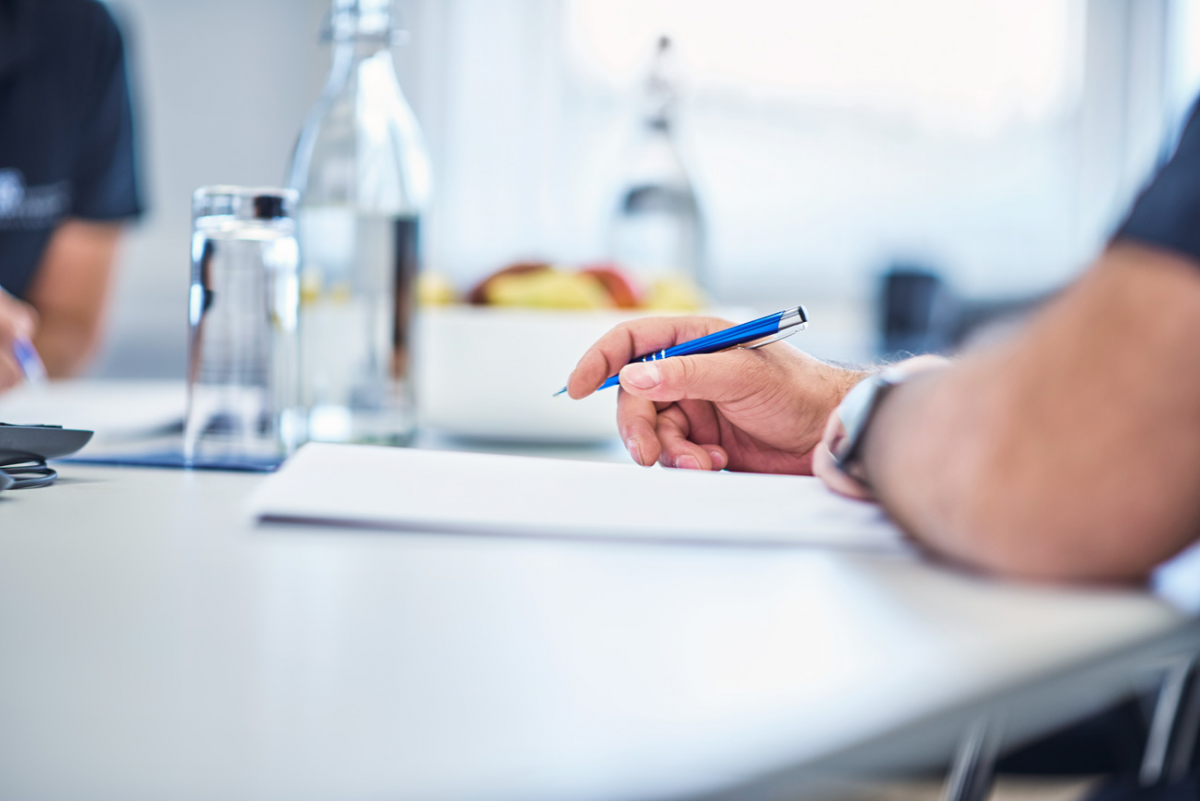
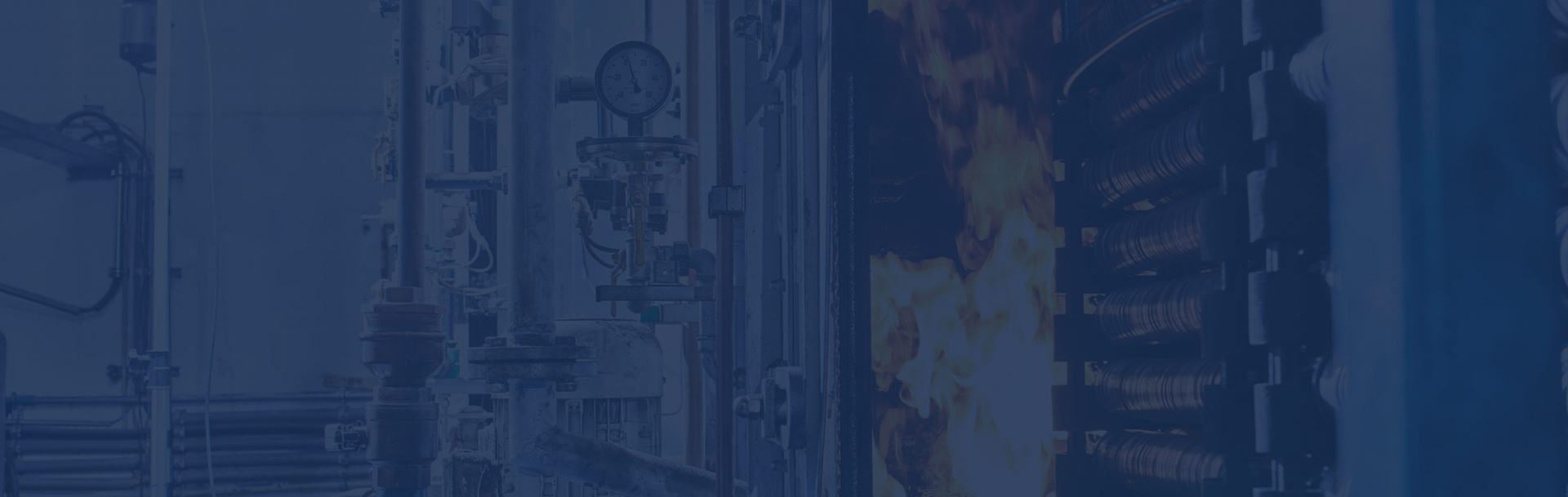
Do you have any questions?
The HTR team will be happy to advise you!