NITRIDING
Salt bath nitriding
In salt bath nitriding, the parts to be treated are treated in a nitriding bath to increase the surface hardness and then oxidised in a quenching bath.
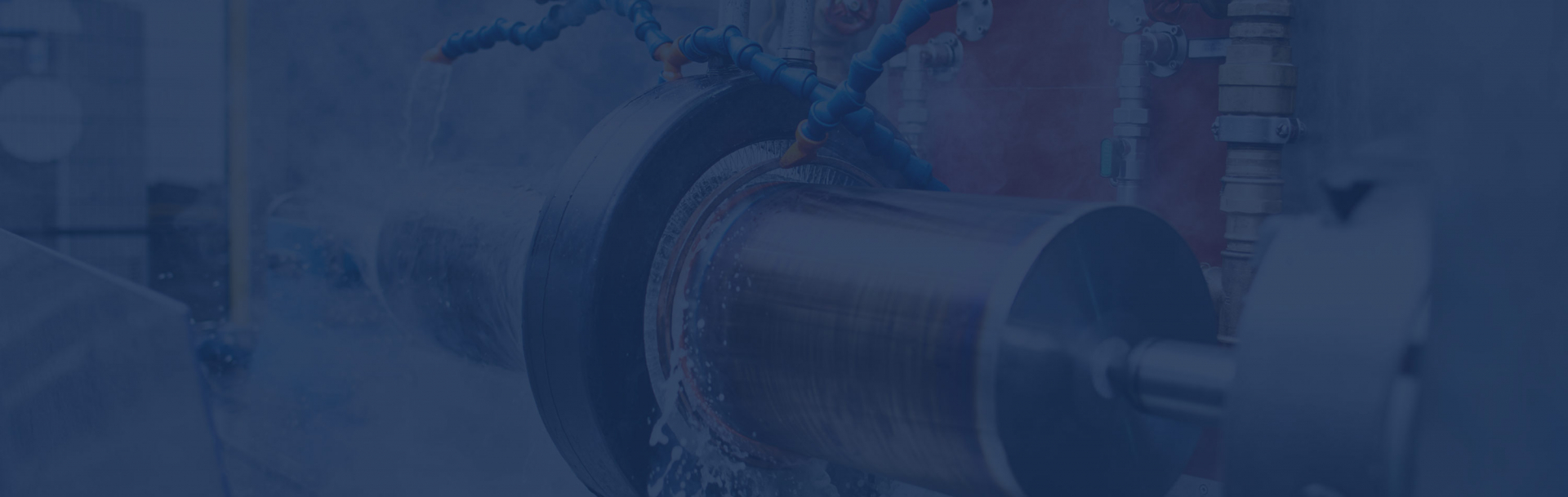
Advantages of the process
No
distortion
Nitriding is the only hardening process in which there is no process-related distortion of the component.
Outstanding
component properties
Nitriding in a salt bath produces wear-resistant components with improved fatigue resistance and high corrosion resistance.
Attractive
appearance
Oxidation in the AB1 bath causes the surface of your components to turn an aesthetic black colour.
First-class hardened components from the salt bath
Nitriding in a salt bath is a chemical-physical process in which a diffusion zone is created on the finished workpiece after heat treatment. For this purpose, the components are preheated evenly to around 350 °C and then immersed in a 580 °C nitriding bath with a controlled cyanide cyanate content. The bath in the liquid molten salt lasts between a few minutes and a few hours, depending on the steel composition and mould.
After the specified treatment time has elapsed, the workpieces are quenched in water, oil or a polymer. In addition to the incorporation of nitrogen, carbon always diffuses into the component surface during salt bath nitriding. This is a key reason for the positive, specific edge zone properties of salt bath-treated components.
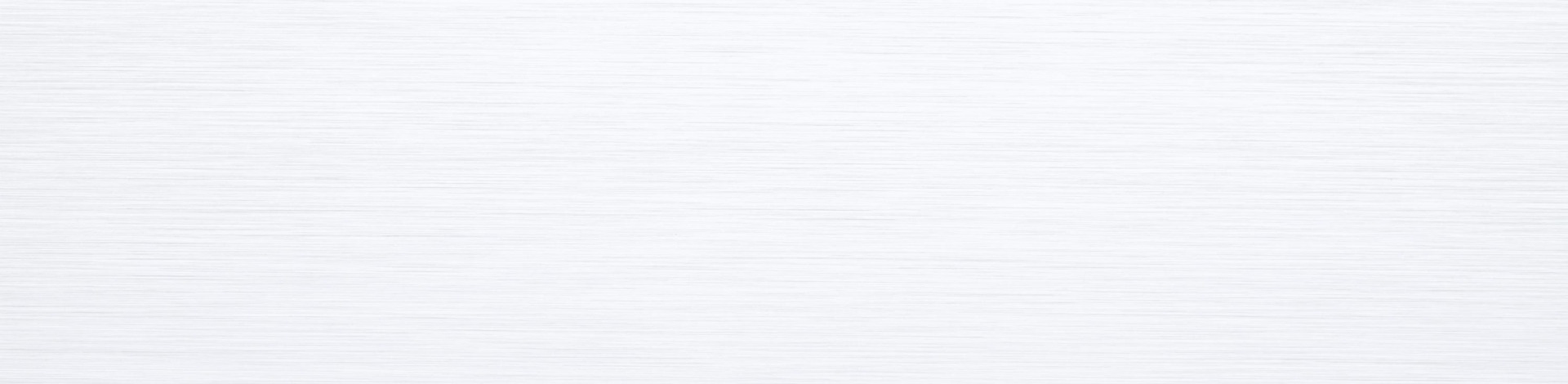
Corrosion resistance can be improved by post-treatment in an oxidising bath, the so-called AB1 bath.
To do this, the workpiece is immersed in an oxidising bath at around 380 °C directly after the nitriding bath and held for 10-15 minutes.
The oxidation neutralises any adhering cyanide and converts it into non-toxic sodium carbonate. The new surface, whose corrosion resistance is in many cases superior to galvanised surface layers, turns an aesthetic black colour.
This is followed by quenching in water with subsequent drying and polishing. Tenifer is suitable for a variety of different materials such as stainless, unalloyed, low-alloy or high-alloy steels, cast iron, ductile iron or sintered metals.
Wear resistance, fatigue resistance and corrosion resistance
Nitriding in a salt bath is widely used, not least due to its outstanding corrosion resistance and attractive appearance. The technique is characterised by a short treatment time and reproducible quality standards.
It is frequently used for components in the automotive industry and mechanical engineering tools in particular. As no structural transformation occurs during salt bath nitriding and the thermal stresses are very low, no significant dimensional changes are to be expected. Wear resistance, fatigue resistance and corrosion resistance increase significantly after salt bath nitriding. These nitrided layers are heat-resistant up to 500 °C and also exhibit high toughness - no damage to the surface can be recognised even after stressing beyond the yield poin
Key figures
Temperature:
up 580°C
Oven size:
500 x 500 x 500 mm
Lead time:
from 1 Woche
Nitriding hardness depth:
up to 0,5 mm
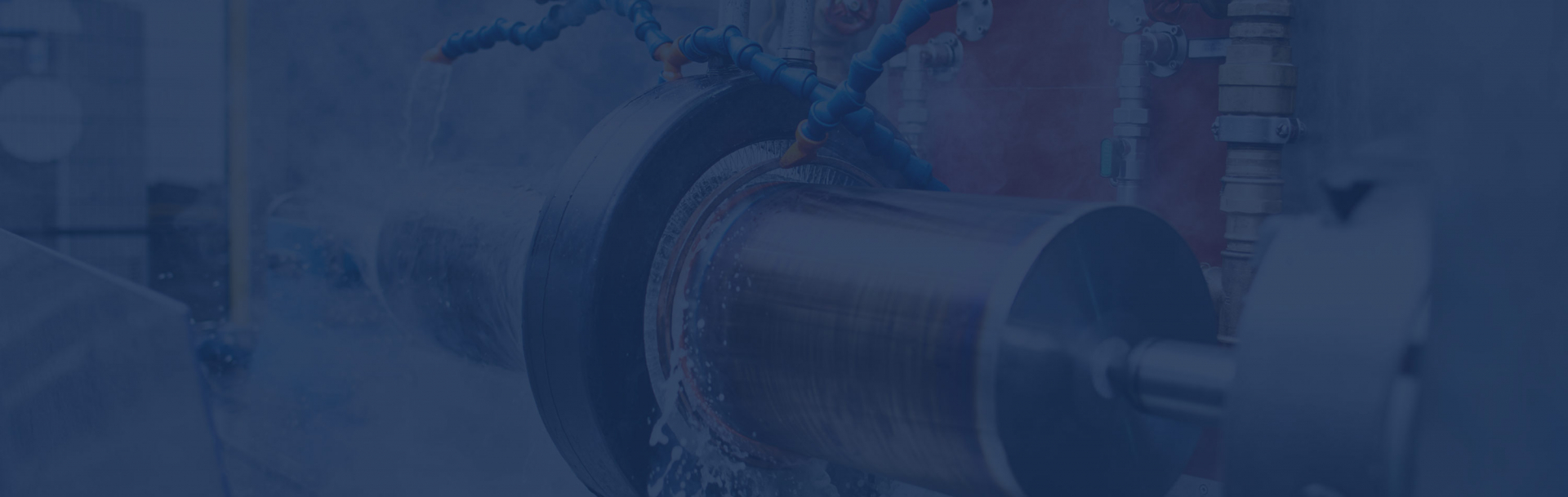
Request a quote
Request a free and non-binding
offer from us now!
Info!
For the preparation of your individual offer
we need the following information from you:
- Material
- Weight and quantity
- Desired surface hardness (in HV) with tolerance field
- Desired nitriding hardness depth with tolerance field
- Test specification
If a determination of the nitriding hardness depth or compound layer thickness is required, a component must be destroyed.
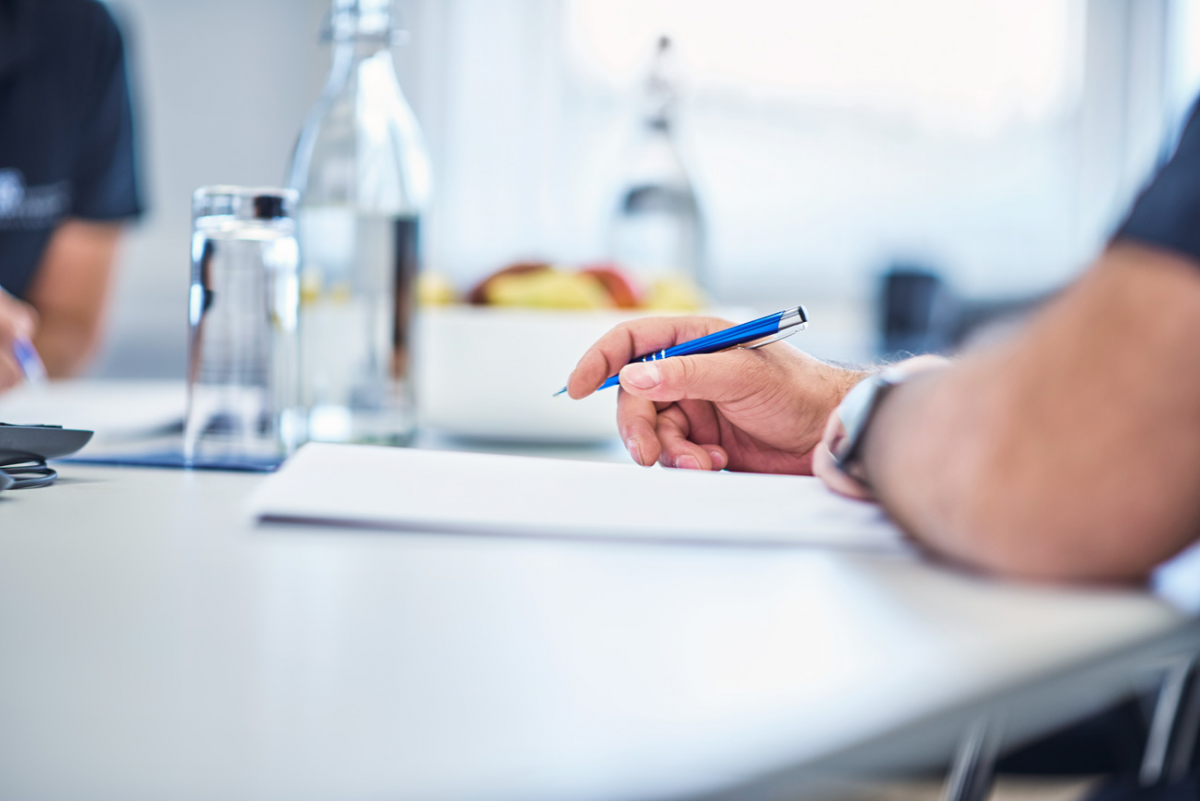
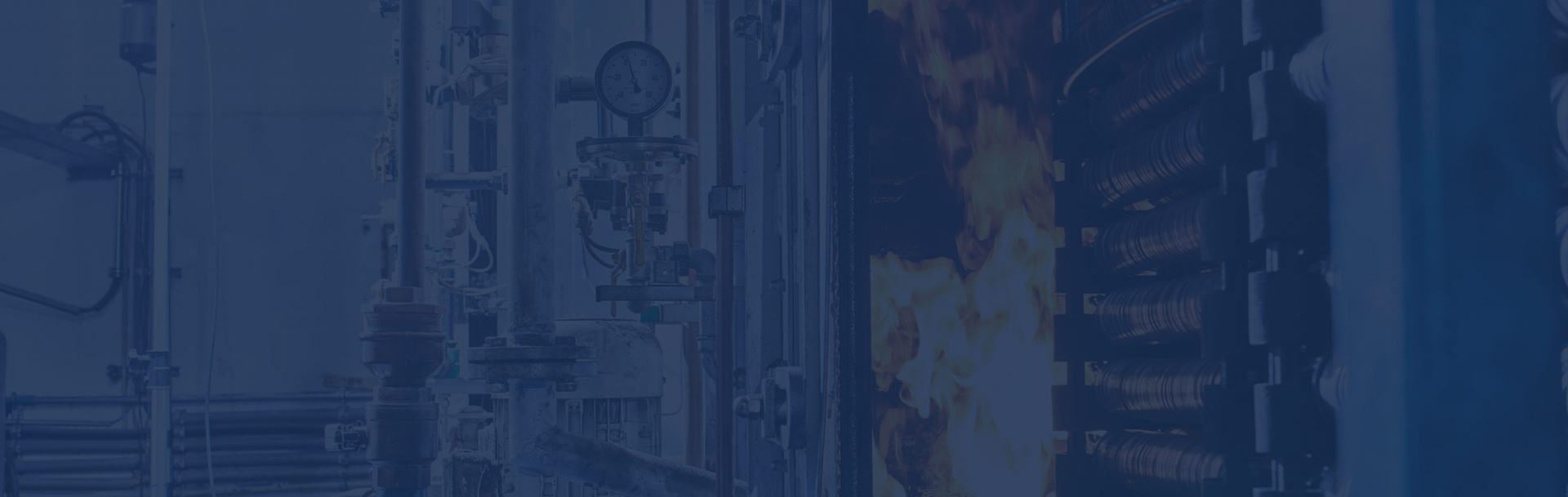
Do you have any questions?
The HTR team will be happy to advise you!